Example 1
Hot Bar Soldering System, Inline design with 3 working stations
Adaption to an Asys linear transport system.
Transport of product jigs is from left to right with automatic indexing of the carriers.
The products that are placed on the carriers are fluxed with our patentedFlux-Applicator in station 1.
A defined amount of flux is applied automatically onto the solder joints in a reliable process.
Flux application is done within a few seconds.
Thus two Hot Bar Soldering stations can follow one flux station.
Both of the two following Hot Bar Soldering Stations are equipped with 3 soldering bars each.
Each soldering bar is controlled separately by the control PLC and, therefore, can be set up differently according to product specifications.
Path sensors at each soldering unit measure the height of the parts and detect the path that the soldering bar sinks into the melting soldering pot.
Additionally force measurement devices monitor the forces that occur at each soldering station during the process.
System is equipped with facilities for communication and data logging (traceability).
Complete project planning, design, construction, installation, commissioning and support.
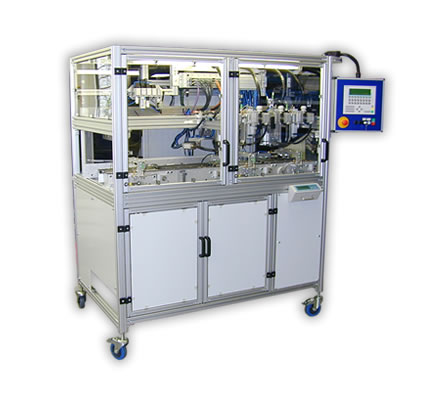